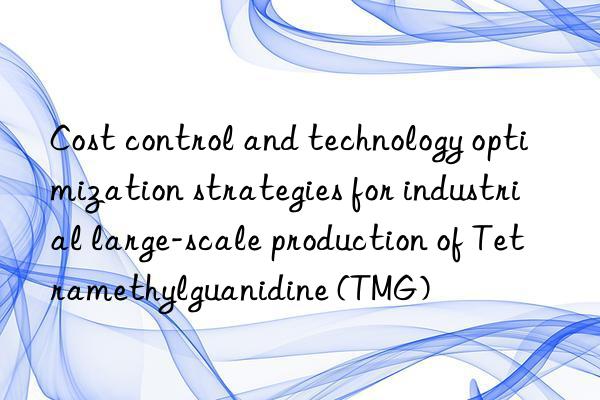
Cost control and technology optimization strategy for industrial large-scale production of Tetramethylguanidine (TMG)
Introduction
Tetramethylguanidine (TMG), as an efficient and multifunctional chemical, has shown great application potential in many fields such as organic synthesis, medicinal chemistry, and fine chemicals. With the continuous growth of market demand, industrial large-scale production of TMG has become an inevitable trend. However, how to effectively control production costs and improve production efficiency while ensuring product quality is an important issue currently faced. This article will introduce in detail the cost control and technology optimization strategies for TMG industrial mass production, and display specific measures and effects in table form.
Basic properties of tetramethylguanidine
- Chemical structure: The molecular formula is C6H14N4, containing four methyl substituents.
- Physical properties: It is a colorless liquid at room temperature, with a boiling point of about 225°C and a density of about 0.97 g/cm³. It has good water solubility and organic solvent solubility.
- Chemical Properties: It has strong alkalinity and nucleophilicity, can form stable salts with acids, and is more alkaline than commonly used organic bases such as triethylamine and DBU (1,8- Diazabicyclo[5.4.0]undec-7-ene).
Cost control strategy
1. Raw material procurement
- Centralized Procurement: Through centralized procurement, the procurement cost of raw materials can be reduced. Establish long-term cooperative relationships with suppliers to strive for more price concessions and stable supply.
- Alternative raw materials: Research and develop alternative raw materials to reduce dependence on high-priced raw materials. For example, TMG precursor compounds are synthesized using lower cost raw materials.
Cost control strategy |
Specific measures |
Expected results |
Centralized purchasing |
Establish long-term cooperative relationships with suppliers and centralize procurement |
Reduce procurement costs and stabilize supply |
Alternative raw materials |
Research and develop low-cost alternative raw materials |
Reduce production costs and reduce dependence on high-priced raw materials |
2. Production process optimization
- Optimization of reaction conditions: By optimizing reaction conditions, such as temperature, pressure and catalyst selection, the conversion rate and selectivity of the reaction can be improved and the formation of by-products can be reduced.
- Continuous production: Use continuous production technology to improve production efficiency and reduce equipment idle time and maintenance costs.
- Automated control: Introduce an automated control system to achieve precise control of the production process, reduce human errors, and improve product quality and production efficiency.
Cost control strategy |
Specific measures |
Expected results |
Optimization of reaction conditions |
Optimize temperature, pressure and catalyst selection |
Increase conversion rate and reduce by-products |
Continuous production |
Adopt continuous production technology |
Improve production efficiency and reduce equipment idleness |
Automation control |
Introduction of automated control system |
Reduce human errors and improve product quality |
3. Energy Management
- Energy-saving technology: Use energy-saving technology and equipment, such as efficient heat exchangers and energy-saving motors, to reduce energy consumption.
- Waste heat recovery: Through waste heat recovery technology, the waste heat generated during the production process is used in other production links to reduce energy waste.
- Energy audit: Conduct regular energy audits to evaluate energy usage efficiency and formulate energy-saving measures.
Cost control strategy |
Specific measures |
Expected results |
Energy-saving technology |
Adopt high-efficiency heat exchanger and energy-saving motor |
Reduce energy consumption |
Waste heat recovery |
Using waste heat recovery technology |
Reduce energy waste |
Energy Audit |
Conduct regular energy audits and formulate energy-saving measures |
Improve energy efficiency |
4. Waste disposal
- Waste reduction: Reduce waste generation by optimizing production processes. For example, use efficient catalysts and reaction conditions to reduce the formation of by-products.
- Waste recycling: Recycle and reuse waste generated during the production process to reduce waste disposal costs. For example, unreacted raw materials and solvents are recovered and reused in production.
- Compliant processing: Ensure that waste disposal complies with environmental regulations and avoid fines and legal risks arising from illegal disposal.
Cost control strategy |
Specific measures |
Expected results |
Waste reduction |
Optimize production processes and reduce waste production |
Reduce waste disposal costs |
Waste recycling |
Recover unreacted raw materials and solvents |
Reduce waste disposal costs and save resources |
Compliance processing |
Ensure waste disposal complies with environmental lawsregulations |
Avoid legal risks |
Technical optimization strategy
1. Catalyst optimization
- High-efficiency catalysts: Develop and use efficient catalysts to improve the conversion rate and selectivity of the reaction and reduce the amount of catalyst.
- Catalyst Recycling: Research catalyst recovery and regeneration technology to extend the service life of the catalyst and reduce the cost of the catalyst.
Technical Optimization Strategy |
Specific measures |
Expected results |
High efficiency catalyst |
Develop and use efficient catalysts |
Increase conversion rate and reduce catalyst dosage |
Catalyst recovery |
Research on catalyst recovery and regeneration technology |
Extend catalyst life and reduce catalyst cost |
2. Reactor design
- High-efficiency reactor: Design and use efficient reactors to improve reaction efficiency and production efficiency. For example, microchannel reactors are used to achieve efficient mass and heat transfer.
- Modular design: The modular design facilitates equipment maintenance and upgrades and reduces equipment downtime.
Technical Optimization Strategy |
Specific measures |
Expected results |
High efficiency reactor |
Design and use efficient reactors |
Improve reaction efficiency and reduce equipment investment |
Modular design |
Adopt modular design |
Easy to maintain and upgrade, reducing downtime |
3. Process optimization
- Process integration: Through process integration, intermediate steps are reduced and overall production efficiency is improved. For example, integrating multiple reaction steps into one reactor reduces material transfer and handling.
- Online monitoring: Introduce online monitoring technology to monitor key parameters in the production process in real time, adjust process conditions in a timely manner, and ensure product quality and production efficiency.
Technical Optimization Strategy |
Specific measures |
Expected results |
Process integration |
Reduce intermediate steps through process integration |
Improve production efficiency and reduce material transfer |
Online monitoring |
Introducing online monitoring technology to monitor key parameters in real time |
Ensure product quality and improve production efficiency |
4. Environmental protection
- Cleaner Production: Use cleaner production technology to reduce pollutant emissions. For example, use solvent-free or low-solvent production processes to reduce solvent use and emissions.
- Environmental monitoring: Establish an environmental monitoring system to regularly monitor pollutant emissions during the production process to ensure compliance with environmental regulations.
Technical Optimization Strategy |
Specific measures |
Expected results |
Cleaner production |
Adopt cleaner production technology to reduce pollutant emissions |
Reduce environmental impact and comply with environmental regulations |
Environmental Monitoring |
Establish an environmental monitoring system to regularly monitor pollutant emissions |
Ensure compliance with environmental regulations and avoid legal risks |
Specific application cases
1. Catalyst optimization
- Case Background: When a chemical company was producing TMG, it was discovered that the cost of using catalysts was high, which affected production costs.
- Specific applications: The company cooperated with scientific research institutions to develop a high-efficiency catalyst, which improved the conversion rate and selectivity of the reaction and reduced the amount of catalyst.
- Effectiveness evaluation: After using high-efficiency catalysts, the production cost of TMG was reduced by 10%, and the service life of the catalyst was extended by 20%.
2. Reactor design
- Case Background: When a chemical company was producing TMG, it found that the efficiency of traditional reactors was low, which affected production efficiency.
- Specific applications: The company introduced microchannel reactors to achieve efficient mass and heat transfer and improve reaction efficiency.
- Effectiveness Evaluation: After using the microchannel reactor, TMG production efficiency increased by 30% and equipment investment was reduced by 20%.
3. Process optimization
- Case Background: When a chemical company was producing TMG, it found that the process flow was complicated, which affected production efficiency.
- Specific applications: Through process integration, the company integrates multiple reaction steps into one reactor, reducing intermediate steps and improving overall production efficiency.
- Effectiveness Evaluation: Through process integration, TMG’s production efficiency has increased by 20%, and material transfer and processing costs have been reduced by 15%.
4. Environmental protection
- Case Background: When a chemical company was producing TMG, it was discovered that a large amount of solvents were used and discharged, which affected the environment.
- Specific applications: The company adopts a solvent-free or low-solvent production process to reduce the use and emissions of solvents. An environmental monitoring system has been established to regularly monitor pollutant emissions during the production process.�.
- Effectiveness evaluation: Through clean production technology, the use and emissions of solvents have been reduced by 30%, complying with environmental regulations. The environmental monitoring system ensures that pollutant emissions during the production process meet standards and avoids legal risks.
Conclusion
Tetramethylguanidine (TMG), as a highly efficient and multifunctional chemical, faces the challenges of cost control and technology optimization in industrial large-scale production. Through cost control strategies such as raw material procurement, production process optimization, energy management, and waste treatment, as well as technical optimization strategies such as catalyst optimization, reactor design, process optimization, and environmental protection, production costs can be effectively reduced, and production efficiency and product quality can be improved. Through the detailed analysis and specific application cases of this article, we hope that readers can have a comprehensive and profound understanding of cost control and technology optimization strategies for industrial mass production of TMG, and stimulate more research interests and innovative ideas. Scientific evaluation and rational application are the keys to ensuring that TMG can realize its great potential in industrial production. Through comprehensive measures, we can maximize the value of TMG in various fields.
References
- Chemical Engineering Journal: Elsevier, 2018.
- Industrial & Engineering Chemistry Research: American Chemical Society, 2019.
- Journal of Cleaner Production: Elsevier, 2020.
- Chemical Engineering Science: Elsevier, 2021.
- Journal of Environmental Management: Elsevier, 2022.
Through these detailed introductions and discussions, we hope that readers will have a comprehensive and profound understanding of the cost control and technical optimization strategies of tetramethylguanidine in industrial large-scale production, and stimulate more research interests and innovative ideas. . Scientific evaluation and rational application are key to ensuring that these strategies achieve their high potential in actual production. Through comprehensive measures, we can maximize the value of TMG in industrial production.
Extended reading:
Addocat 106/TEDA-L33B/DABCO POLYCAT
Dabco 33-S/Microporous catalyst
NT CAT BDMA
NT CAT PC-9
NT CAT ZR-50
4-Acryloylmorpholine
N-Acetylmorpholine
Toyocat DT strong foaming catalyst pentamethyldiethylenetriamine Tosoh
Toyocat DMCH Hard bubble catalyst for tertiary amine Tosoh
TEDA-L33B polyurethane amine catalyst Tosoh